A fresh look at a lighter, greener tail cone
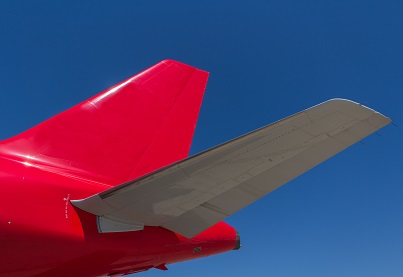
New environmental requirements have led the aviation industry to explore new approaches to aircraft development and manufacture for decreased fuel consumption, emissions and noise.
The EU-funded project ADVITAC targeted the development of a greener aircraft tail cone. The cone plays a critical role in aircraft structure and function. It also contains an aircraft’s auxiliary power unit (APU) – used to provide cabin air on the ground, pneumatic pressure for engine starts, and primary or back-up electrical power for an aircraft’s systems.
ADVITAC, which ended in November 2012, developed new architecture, design concepts and manufacturing processes with the aim of creating a cheaper, thinner integrated tail cone. The goal was reduced aircraft noise and fuel consumption.
The project tested the new techniques by building a demonstrator tail cone for regional and business aircraft made of composite material, and using an advanced infusion manufacturing process. Under this new method, a dry fabric is preformed into a mould that has the component’s shape, then infused with resin and cured.
The team made huge leaps in advancing understanding of composite tail cone design and the resin infusion process for manufacturing large parts, despite technical difficulties encountered when making the demonstrator, says project coordinator Michael Hugon of Daher in France.
“The project consortium gained valuable experience of low-cost equipment solutions for the infusion of large parts, tail cone acoustics, electrical systems, and reinforced assembly techniques,” he says. “These are major steps that will determine the directions to be adopted with regard to the technologies of the future.”
Learning by doing
While the project achieved a small reduction in weight and cost, ADVITAC’s partners concluded that until infusion technology is developed further and becomes easier to control, the method is not appropriate for making tail cones.
But with new types of resin and processes it could be a green way to manufacture tail cones in the future, says Hugon.
“The team achieved a major increase in efficiency regarding low-cost tools for resin infusion of composites, a sensitive process previously lacking in reliability required for real industrial applications,” he adds. “We learned a lot but it’s a process that still needs improvement.”
Other project partners also benefited from the research, including small to medium-sized enterprises. For example, Coriolis Composites in France was able to test and improve its dry fibre placement process for manufacturing composite parts for aircraft, he says. The method, which is used to reinforce structures, enables manufacturers to produce extremely light and rigid parts.
Spain-based Tecnalia tested nanotubes as a means of increasing the electrical conductivity of composite laminates to protect aircraft from lightning strikes. Normally bronze wire mesh is incorporated in composite materials to create a conductive path and protect the aircraft from damage, but this method is costly and adds weight to aircraft. The nanotubes did not perform as required.
“Now we know nanotubes do not work,” says Hugon. “While the results are a disappointment, they indicate we need to find other solutions.”
He notes that Daher also benefited from the project by increasing its understanding of composite materials, and through working with a group of “innovative and efficient partners”.
He adds: “The project was a wonderful way to demonstrate European innovation capabilities to end users.”