Labels to show how retreaded tyres stack up against new tyres
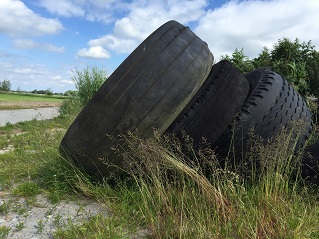
Related topics
Innovation SMEs Transport Innovation in SMEs Smart, green and integrated transport Austria Czechia Germany Italy Netherlands Spain United Kingdomdate: 02/07/2015
Project: Classification of retreaded truck tyres ...
acronym: RETYRE
See also: CORDIS
When a tyre wears out, vehicle owners have a choice: they can replace it with a new tyre – or with a retreaded tyre. Retreaded tyres use the metal casing of an old tyre but replace the worn-out rubber with a new rubber tread.
New tyres already have a simple label grading rolling resistance (for fuel efficiency), wet braking (for stopping distance) and (rolling) noise emission – resembling eco-labels for electrical goods. The EU-funded ReTyre project has developed a method to classify retreaded truck tyres in the same way. Transferred to labels, this data could give commercial consumers and end-users an objective way to choose between all tyres on the market and creates a level playing field for new and retreaded tyres for the three values.
The coordinator of the 15-member project is Ruud Spuijbroek, Secretary General of the European retreaders’ association BIPAVER. He says: “We need a label for our customers, who are often haulage and transport companies. They want to compare tyres, as well as know-how, to combine them for the best performance from a truck.”
Up to 50% of tyres for commercial vehicles are retreaded to save money and avoid waste. The result is an industry that employs around 18 000 people in Europe.
Retreading a tyre maximises a casing’s lifespan and uses 70% less new material and 80% less energy than manufacturing a new tyre, making it good for the planet too, says Spuijbroek.
BIPAVER represents independent retreading SMEs. Their members feared that without an objective comparison to new tyres, customers would be prejudiced against retreaded tyres.
ReTyre developed a system to assess the performance and environmental impact of casings, treads and retreading processes, using internationally-recognised standard tests. Applying this data, it has built the first phase of an internet-accessible program for retreaders, to produce EU-regulation-compliant data for retreaded tyres.
Supporting consumers and SMEs
The type of tread and retreading method affects a tyre’s performance. Less depth of tread reduces rolling resistance and noise, while deeper treads and more pattern give better grip, shorter stopping distance and more mileage. The replacement tread itself can be either moulded in advance (“cold re-treading”) or moulded directly on the casing (“hot retreading”). Cold retreading often produces a better performance but incurs higher costs.
“The problem was that retreading businesses had a good retreading method and lots of experience, but no objective data on performance,” says Spuijbroek. This was due to the steep cost to individual companies of testing the over 8 000 possible casing and tread combinations. “We had to make and test all combinations separately,” he adds.
Once the testing data was ready, the 30-month project developed a program to process specifications for the casing, the tread (its compound and pattern) and the retreading method to give performance data for a specific retreaded tyre.
Spuijbroek says: “The project’s journey was very interesting and brought together companies that are usually competitors – our solution needed the input of retreaders, scientists, and mathematicians.”
He hopes that the testing methods and standardised database information developed by the project will help the retreaded tyre industry comply with future consumer and environmental protection regulations.
Retreaders can access the program through the BIPAVER site. Although ReTyre has now ended, the project team would like to continue to expand the database with data on the different chemical compounds used for the rubber treads, continuing the project’s work to support retreading SMEs.
Applying a new tread in the "cold" retreading procedure; Testing rolling resistance
© BIPAVER
Cold retreading; Testing drum
© BIPAVER