Anticipating the future of predictive maintenance
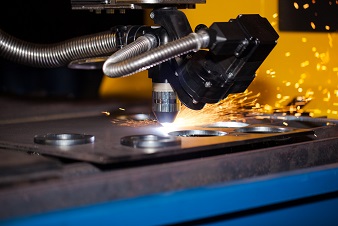
Related topics
Industrial Technologies Innovation Industrial Leadership Leadership in enabling and industrial technologies Czechia France Germany Poland Spaindate: 30/06/2015
Project: SUstainable PREdictive Maintenance for m...
acronym: SUPREME
See also: CORDIS
The Supreme project has produced a highly advanced predictive maintenance system. This cutting-edge solution is underpinned by three modules, respectively designed to monitor individual machines, anticipate failures, and optimise settings.
While these modules can operate in isolation, the full added value arises from their interaction in the integrated system developed by the partners, says project coordinator Sophie Sieg-Zieba of CETIM (Technical Centre for the Mechanical Industry), France.
The modules draw on a variety of signal and data processing tools and techniques, which the partners developed or improved as part of the project. The new system was tested in a paper mill and could be adapted for use in many other sectors, Sieg-Zieba notes.
A finger on the mechanical pulse
The enormous machines used to make paper are sophisticated pieces of equipment. They handle all the production steps required to transform pulp into reels of pristine product.
The machine used in the Supreme case study was one such giant. “It runs 24/7,” says Sieg-Zieba. “It is really important to avoid any unplanned downtime and to keep the production level as high as possible.”
To do so, Supreme has devised a solution involving three IT modules and a framework that enables them to interact. One of these modules monitors the condition of the machine based on readings taken by sensors, some of which were specifically developed by the project.
Another module helps operators to identify individual components that could stall production if they were to break down, and works out how these parts are likely to wear. It then injects this information into the maintenance schedules to ensure that predictable failures can be avoided.
Mind the machine
The third module enables users to optimise the operation of the machine for key parameters. It can, for example, highlight the best settings to use with regard to energy efficiency.
Modules such as these are already used in some applications, but are usually run independently. One of the main achievements of Supreme lies in combining them, says Sieg-Zieba. This innovation, she explains, paves the way towards automatic and dynamic scheduling of predictive maintenance, eliminating the need for operators to process the information manually on a case-by-case basis.
In addition, the partners found ways to develop and improve the functionalities of each individual module, and the complete system was then trialled on the paper machine. Initial findings indicate that the partners have met their objective of reducing energy consumption, environmental cost and downtime for this particular machine by more than 5%, she notes, but final figures have yet to be calculated.
Analysing the results of the test is one of the tasks that remain to be completed before the project ends in August 2015. The partners are also putting the final touches to a number of e-learning modules dedicated to the new system, and they are preparing documentation that will explain how to adapt their predictive maintenance solution to other types of machine. Paper making is just one of many industrial processes the Supreme system could help to improve.