The fine art of nanotech
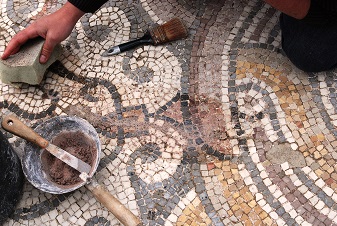
date: 23/06/2015
Project: Nano-materials for the conservation and ...
acronym: NANOFORART
See also: CORDIS
Each of the many different substances used to create art need specially adapted conservation products to clean and preserve works safely. Traditional products often have their limitations, involving layers of incompatible coatings, relying on toxic, harsh solvents, or harming water-sensitive materials such as paper or leather.
The NANOFORART project used nanotechnology to engineer safer conservation products. Designed for art made with traditional media, such as frescos, drawings or oil paintings, the products incorporate low-toxicity nano-dispersions (suspensions), micro-emulsions and specially-engineered cleaning gels.
Project manager Piero Baglioni of Italy’s Research Center for Colloids and Surface Science explains that researchers in the EU-funded project already had an academic interest in using nanoscience to care for art.
They wanted to develop environmentally-friendly, professional-quality products that use very few solvents. Although nanotechnology has now arrived on the art conservation scene, the complexity of developing these products and the small size of their potential market mean that there is limited investment in creating safer products.
It was also important to promote processes that respect the original composition of artefacts. “The best conservation methods try to avoid changing or adding to a work,” says Baglioni.
Inspired by other nanotechnology-based products, such as gels for cleaning contact lenses, the team transferred this science to new conservation products. Fifteen specialist conservation formulations and chemical hydrogels, which can be adapted to different tasks, resulted.
“Our impact assessment by toxicology experts from Venice University showed that the products are safe for the environment and for people using them,” says Baglioni. Other tests confirmed that the products do not damage art, during restoration or longer-term. This reduces the risk and disruption that are common in conservation, making it easier to keep masterpieces looking as they were intended to look.
Baglioni points out that NANOFORART’s products can also save money: these restorations last longer than those carried out using traditional products, and they are safe enough for tourist sites to remain open during the work.
Science meets art
Through tweaks to existing nanotechnology formulations, four new classes of preservation and cleaning products emerged, each with their own conservation advantages:
- Nanoparticle dispersions that stabilise damaged plaster, marble and other carbonate materials. Small losses in the work’s surface are filled in with chemically-similar nanoparticles, producing more permanent, compatible restoration than when traditional stabilisers are used.
- Alkaline nanoparticle dispersions that limit acidification of paper, parchment and leather. The very small particles penetrate through the work better than those in traditional de-acidification products, while water-vulnerable artefacts can be treated using an alcohol-based product.
- Oil-in-water micro-emulsions that remove grime and old coatings safely from fixed art. Containing only 5-25% solvent oils, they are much less toxic and release much less dirt back into the art than fully oil-based cleaners.
- Thin layers of gel that clean oil paintings. These apply precisely-controlled amounts of cleaning fluid directly to the work, without damaging the picture or leaving residues.
High-tech molecular analysis allowed the lab researchers to further optimise safety, stability and performance. Trained staff at museums and conservators participating in the project then examined the products’ performance in everyday restoration practice, suggesting fine-tuning where needed.
A larger-scale production process was developed for the final products to demonstrate their suitability for manufacturing processes. The prototypes are trademarked but are ready for commercialisation by SMEs.
Guidelines on using the products and two published books on conservation methodologies complete the project’s support for museums and conservators. Research data has also been published in several journals.
Project members have now applied for Horizon 2020 funding for a new project – NANORESTART – that adapts their products to modern art materials such as acrylics and plastics, which decay more quickly than traditional materials.
Fresco from the S. Cristoforo church in Milan before cleaning and restoration and after cleaning with a NANOFORART microemulsion
© The Royal Society of Chemistry 2014