Innovative materials to make life lighter
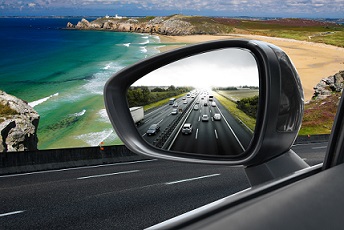
Related topics
Innovation Transport Industrial Leadership Societal Challenges Smart, green and integrated transport EU countries Austria Belgium France Germany Italy Spain United Kingdom Switzerland Nanotechnologies, advanced materials, advanced manufacturing & processing, and biotechnologydate: 22/04/2015
Project: Advanced materials enabling HIgh-VOlume ...
acronym: HIVOCOMP
See also: CORDIS
While light-weight, high-performance composite materials such as carbon-fibre-reinforced plastics already exist, production volumes tend to be limited to a few hundred or a few thousand units per year for aerospace or sports car applications.
The HIVOCOMP project aimed to change that by developing two new kinds of material for the automotive industry and for suitcases.
A breakthrough resin suitable for cars made for the mass market
One strand of the project was dedicated to thermosetting composites on a polyurethane base – a novel composite resin chemistry developed by Huntsman Polyurethanes, one of the industrial partners working on HIVOCOMP – particularly suited to cars produced at high volumes (100 000+ units per year). This material is liquid or at least malleable before it is moulded and sets in its final form. While polyurethane is used in many different applications, it is rather unusual as a matrix for carbon-fibre composites, where epoxies (a type of resin) are more common.
“The main challenge in the thermoset matrices was to drastically reduce production time for the product, while keeping the properties on the level of automotive standards, meaning it has to have a high use-temperature to withstand the existing body painting process and still a good toughness for crash resistance,” explains HIVOCOMP’s scientific coordinator Ignaas Verpoest of Katholieke Universiteit Leuven.
Cutting weight by up to 40%
The consortium was able to build demonstrators where structural parts of a car, such as the inner-bonnet or the B-pillar between the front door and the back door, were made of the new material.
The ease and speed of processing of this novel resin make it possible to produce composite (semi) structural parts for vehicles at high volumes
The weight reduction potential varies, depending on the specific application. “The more complex and the smaller the part, the smaller the potential weight reduction. If you have a large part with fewer connections where the material as such plays a large role, the weight reduction can go up to 25% or even 40%,” says Verpoest.
Innovative hybrid material
The second project strand focused on suitcases made from self-reinforced polypropylene, although the same material was also used to produce a car part demonstrator in the form of a rear seat. Contrary to the carbon-fibre technology, suitcases such as those by well-known manufacturer Samsonite – another HIVOCOMP partner – are currently made of said self-reinforced polypropylene, i.e. polypropylene fibres in a polypropylene matrix.
The University of Leeds originally developed this material, which is extremely light and impact resistant, even at relatively low temperatures, more than 20 years ago. But HIVOCOMP took its advantages one step further. “We tried to increase the stiffness of the material, because it is rather floppy and deformable. And for certain applications that was not sufficient,” Verpoest points out.
“The idea was to add between 10% and 15% of carbon fibres – not 50% as in the polyurethane-based composite. That is a completely new thing, and the University of Leeds together with the University of Leuven have had this new hybrid material patented.”
Again, HIVOCOMP built a demonstrator, a unique suitcase, which indeed displays a higher stiffness than a traditional model, but still has the same resistance. Despite the improved performance, it can still be produced in high volume, because HIVOCOMP stuck to the original production process, namely thermoforming, which involves heating a plastic sheet until it is pliable and then forming it to the desired shape in a mould and trimming it..
Successful results with high impact
“It has been a really successful project, accelerating innovation and producing truly breakthrough materials that really serve the needs of the end-user industries,” HIVOCOMP project manager Harilaos Vasiliadis of consultancy firm Bax & Willems summarises. “In the past, similar innovations would have taken perhaps 2-3 times more time – and resources – to bring to the market and with greater risk of failure.”
Samsonite is now looking into putting this new material to use in a new generation of even lighter suitcases, while Huntsman Polyurethanes, as the project partner exploiting the polyurethane-based composite, is in talks with the automotive industry to investigate potential applications.
“Up until now, one of the main stumbling blocks has been the production of carbon-fibre-reinforced composites, which is too low in volume to be cost-efficient,” Verpoest reiterates. “We clearly showed that you can reduce the processing time while keeping up the performance. And this should really help these materials penetrate the market at the end of the day.”