How smart materials could transform shipping in the EU
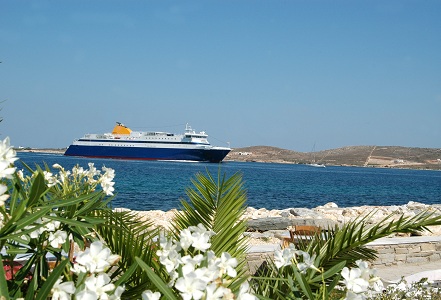
Related topics
Innovation Transport Smart, green and integrated transport Croatia Estonia Finland France Germany Italy Netherlands Romania Spain Sweden United Kingdomdate: 20/02/2015
Project: Adaptive and smart materials and structu...
acronym: ADAM4EVE
See also: CORDIS
Europe’s shipbuilding industry is a dynamic and competitive sector of great economic and social importance. There are currently around 150 large shipyards in Europe, with around 40 active in the global market for large sea-going commercial vessels. Around 120 000 people are directly employed by shipyards in the EU. Yet stiff global competition, particularly from East Asia, has put pressure on the sector to produce smarter products and become more cost-efficient.
The EU-funded ADAM4EVE project, which began in January 2013, has sought to address this challenge by identifying and developing smart materials that could be adapted to maritime needs.
Smart materials and adaptive structures can change their properties or function in a predictable manner as a result of outside forces and environmental influences, allowing ships to react more flexibly to changing operational and environmental conditions, without the need for retrofitting.
Why ships need to be more flexible
“Ships operate in difficult and ever-changing environments,” explains Frank Roland, Managing Director of the Centre of Maritime Technologies (CMT) in Hamburg, Germany, which is coordinating the project. “Typically they tend to be built for a range of specific operational conditions, which can change over their lifetime. Fuel prices, as we have seen, can go up or down, can affect operational decisions (going slower saves fuel), while some vessels like ferries prefer to go slower and quieter at night, so that passengers can sleep.”
Adapting to changing operational scenarios requires retrofitting the dock, and this can be expensive. Roland points out that for a cruise ship costing €600 million, the operator can expect to spend the same amount during the vessel’s lifetime in retrofitting.
“This is where our project began,” he says. “We thought that if we built more flexible ships that could adapt to a wider range of different scenarios, huge savings could be achieved. This would greatly benefit shipbuilders and operators in what is a hugely competitive global environment.”
Introducing the era of smart shipping
After identifying suitable smart materials, the project focused on their applicability. “We matched the ideas of the material developers to the needs defined by leading producers of five ship types made in Europe – cruise ships, ferries, RORO (roll-on-roll-off vessels designed to carry cargo), inland waterway vessels and yachts,” says Roland. “We then set about building prototypes to demonstrate the technical feasibility of our ideas.”
Smart materials have been used to improve the ship’s performance as well as reduce the amount of energy needed for heating, cooling and passenger comfort. Taking inspiration from how aeroplanes extend their wings before landing, the team developed a prototype manoeuvrable rudder and an extendable trim wedge capable of automatically adjusting, depending on varying manoeuvring conditions, service speeds or loading conditions.
Inside the ship, adaptive technologies have been developed to reduce engine vibration. Smart windows and coatings used to control temperature and save energy have also been tested. “Cruise ships and ferries have big windows, which means the rooms behind can get hot if there is too much sun,” explains Roland. “We developed prototype windows that darken depending on the amount of radiation hitting the glass.” The project recently held a workshop for SME glass manufacturers to inform them of this potential new market opportunity.
Materials with heat storage capacities, already partly used in buildings, will further help to reduce the substantial energy demand for air conditioning in passenger vessels.
Finally, the third element of the project, due for completion in December 2015, involves assessing smart materials for their technical feasibility and economic and environmental sustainability. “Additional projects are now needed to take this to the next level and bring these innovations to market,” says Roland.