Paints for places where a spark spells trouble
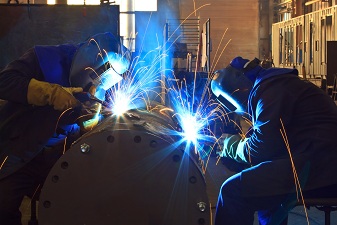
Related topics
Innovation SMEs Innovation in SMEs Advanced materials Cyprus Poland United Kingdom Nanotechnologies, advanced materials, advanced manufacturing & processing, and biotechnologydate: 12/01/2015
Project: Development of film and coating products...
acronym: TRANSCOND
See also: CORDIS
Contact: Contact
The EU-funded TransCond project developed a range of sprayable, transparent and conductive coatings and paints for industrial sites where an errant spark could lead to a fire, explosion or damage to electrical equipment.
The project’s partners, including three small to medium-sized business (SMEs) from the UK, Cyprus and Poland, developed the new paints to replace conventional coatings normally used in such areas.
After the project ended in October 2013, the SMEs launched commercial products for the market, says project coordinator Tadeusz Spychaj, a chemistry professor at West Pomeranian University of Technology in Poland.
“Such next-generation conductive coatings technologies are needed to meet the growing market needs for good quality products that are cheaper, environment-friendly and safe,” he adds. “The new TransCond products will help the three SMEs compete in a growing and increasingly competitive market.”
Cheaper and better coatings
Conventional coatings used in hazardous areas are usually made with metals fillers such as silver, nickel, copper or indium tin oxide, which are expensive and difficult to recycle. The metal fillers are mixed with highly volatile solvents, which pose a potential health risk to humans if inhaled.
TransCond developed a way to make the new coatings, paints and varnishes from carbon nanotubes and graphene, replacing the metals and solvents. Carbon nanotubes and graphene have extraordinary mechanical, electrical and thermal properties and can improve the hardness, electrical and thermal conductivity of conventional polymeric coatings.
The ‘Holy Grail’ of coatings performance, and TransCond’s main achievement, was to develop antistatic coatings 10 times more conductive than conventional coatings, while maintaining 80-90% transparency for applications in polymer lighting and displays, says Spychaj.
The new coatings can be used to cover machine parts, oven doors, protective screens, walls and floors. All meet EU standards for use in explosive environments, or in places where the build-up of static electricity might pose a problem.
For example, a new spray coating was developed for industrial lighting that is transparent and can be applied using a spray gun or brush. This allows customers to retrofit current safety covers for lighting fixtures themselves rather than replace them – saving money.
Another coating can be put on the doors of industrial ovens used to dry printed circuit boards. These boards are easily damaged by static electricity. The coating can also be applied elsewhere, such as on floors, to prevent static electricity from building up as people walk over them.
Other films and coatings include a water-based semi-transparent acrylic varnish for glass and plastic; a semi-transparent waterborne polyurethane coating for glass and plastic; and coloured waterborne acrylic paints – for metallic and plastic materials.
“All the conductive coatings could deliver huge costs savings for companies in the food, electronics, pharmaceutical and petrochemical industries,” says Spychaj.
Since the end of the project, the TransCond products have been widely promoted and the manufacturers in the project have received many enquiries from around the world, he adds.
He believes the companies can capture 5% of their selected target markets within the next two years, collectively increasing their revenues by up to €1 million.