Lighter and cheaper aircraft parts on course for industry take-off
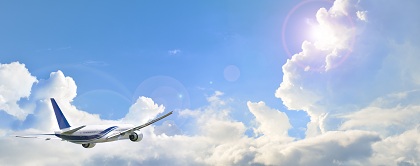
Related topics
Innovation Transport Smart, green and integrated transport Belgium France Germany Greece Italy Sweden United Kingdom Israeldate: 09/12/2014
Project: Simulation based solutions for industria...
acronym: INFUCOMP
See also: CORDIS
Contact: Contact
The aerospace industry uses composites – materials made from two or more separate materials – for their superior strength to weight ratio and resistance to fatigue. Composite aircraft parts are conventionally made using a tape-laying process that involves the placing of sheets of pre-impregnated fibre-resin systems layer-upon-layer to create a laminate in a mould. This is then cured under high pressure in an oven to form the final structure. The process – start to finish – is expensive and time-consuming.
The alternative technology investigated by the four-year INFUCOMP project involves infusing the resin after the dry fabrics have been assembled. The manufacturing costs are lower and materials have a much greater shelf life. This Vacuum Assisted Resin Infusion (VARI) process requires only ‘one-sided tooling’ to hold the part in place, while vacuum membranes are used to consolidate the composite, explains INFUCOMP project coordinator Anthony Pickett of Germany’s Engineering Systems International (ESI).
A major benefit is the ability to produce very large parts while avoiding the complex and costly equipment often required for other liquid composite moulding (LCM) processes used in industry.
Minimising trial and error testing
The INFUCOMP project also developed simulation software that significantly reduces the need for trial-and-error prototype manufacturing. For example, air voids can be identified and then minimised before a part is built, improving part quality and performance.
“Simulations of both small and large-scale prototype structures were carried out for components of aircraft wings and fuselage structures using the new VARI techniques and multi-processor software,” says Pickett. Numerical predictions were closely correlated to prototype test results and were able to predict infusion defects and resin flow, he explains. The software was then used to eliminate these defects and optimise the infusion strategy.
Since the project formally wound up in autumn 2013, the INFUCOMP team has continued to develop the simulation tool, known as PAM-RTM. “Most new developments are projected to be incorporated in the official version 2015, due next year,” says Pickett.
Precision modelling
VARI simulation at the scale of aircraft parts is so huge that it requires more than one computer/processor. The INFUCOMP team therefore looked at the feasibility of applying parallel computing – the use of two or more processors to solve a single problem.
This meant that models comprising several millions of elements could be viewed, dramatically reducing costs compared to previous analysis capabilities. Parallel computing also allowed full 3D simulation, providing a detailed analysis of the resin filling at every stage of the infusion process. This offers new opportunities to identify potential process defects before they occur. The procedure can then be optimised prior to making big investments in tooling.
By the time the research is finalised next year, Picket expects the INFUCOMP team to have made it possible to simulate the manufacture of aircraft structures using infusion technologies, meaning increased payloads and reduced fuel emissions. He then expects other industries, including car manufacturers, to line up to use the technology.
“Further developments of these techniques include compression moulding which is of particular interest for composites manufacturing in the car industry,” says Pickett.