Repairing wind turbine blades at dizzying heights
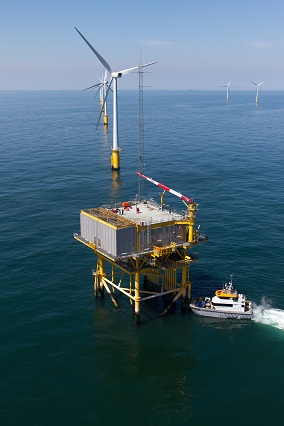
Related topics
Energy Innovation SMEs Innovation in SMEs Secure, clean and efficient energy Advanced materials France Greece Poland United Kingdom Nanotechnologies, advanced materials, advanced manufacturing & processing, and biotechnology Turkeydate: 03/12/2014
Project: Adapted Composite Repair Tooling for in-...
acronym: CORETO
See also: CORDIS
Contact: Contact
According to the World Wind Energy Association’s half-year report 2014, wind energy production now covers around 4% of total worldwide electricity usage, and it is an expanding sector. That means that more and more rotor blades will require maintenance and repair.
Wind turbine blades – made of strong materials such as glass-fibre, carbon-fibre reinforced plastics, and kevlar – are exposed to immense stresses and strains, from exposure to sunlight to lightning strikes. The result: fibre-cracking, fatigue, and degradation. Like any appliance, most rotor blades come with a warranty, but these only cover one to two years after installation. The blades themselves are expected to last anywhere between 15 and 20 years, but what to do if repairs are needed? This was question behind the CORETO project.
Traditionally, specialists would dismantle the turbine blade in need of repair and transport it to a specialised facility. This requires a considerable logistical effort and blade replacement will take an average of five weeks.
Sky-high savings
The CORETO consortium took a different approach: it aimed to create a complete on-site scanning and repair system that could drastically reduce repair time – and hence downtime – to between 2.5 and 4.5 days. The partners estimate that wind farm operators using the system could cut their production losses by about €45 000 per repair for large turbines, based on an electricity price of €0.03 per kilowatt hour (kWh).
An inspector climbing onto the wind turbine blade would carry a small, lightweight testing device known as an ultrasonic transducer to scan for flaws in the material. This transducer – or sensor – does not require any cutting or other destructive sampling, but detects damage using ultrasonic waves in a non-destructive way. This technique is commonly applied in car and aircraft manufacturing, as well as in the aerospace industry.
Fixing the damage
Once the system locates the damaged area, the specialists would prepare the surface by cutting out a section of the blade around the damage. The CORETO team found a mechanical cutting tool to be more appropriate than other methods investigated. While mechanical preparation could result in damage to the fibres of the blade, the project partners believe that technicians and engineers would find it easier to use.
After preparing the surface, the team would use a technology from the aerospace industry specially adapted to the wind turbine industry: a combined heating and vacuum bag instrument.
The team therefore developed blankets customised for heating different areas of the blade, and a combined heating-vacuum bagging device. With the vacuum bag sealed over the damaged area, the composite material needed to fix the damage, such as carbon-fibre, can be applied and moulded to the blade, leaving it once again with a smooth and operational surface.
The CORETO team has already tested its novel technology under lab as well as in workshop conditions, and the results are promising. More work is however needed before full commercialisation, says Hassam Miabhoy, project coordinator at InnoTecUK.
Applications in different areas
“All these results can be utilised in the wind turbine industry, but we have also seen that there is a potential market for this in the rail industry, especially in terms of the non-destructive inspection and testing technology developed within the CORETO project,” comments Miabhoy.
It would be difficult to say when all the systems developed will be fully market-ready, stresses Miabhoy. But key players from the industry have already shown interest following the extensive dissemination work carried out within the project by the partners.