New surgical tool minimises cross-contamination risk
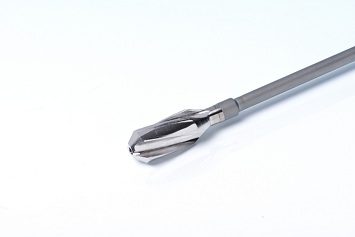
Related topics
Health Innovation SMEs Innovation in SMEs Health, Demographic Change and Wellbeing Advanced materials Germany Italy Netherlands Sweden United Kingdom Nanotechnologies, advanced materials, advanced manufacturing & processing, and biotechnologydate: 03/12/2014
Project: Crevice-free, high reliability bi-metall...
acronym: CLEANTOOLS
See also: CORDIS
Contact: Contact
To make room for that nail, surgeons use an ‘intramedullary reamer’ to drill deep into the marrow cavity of the bone. The tool can ream along the natural curvature of the bone.
In surgery, the reamer's shaft bends as needed. The problem is that bending opens up the shaft in places, similar to what happens when a spring is bent, potentially allowing blood and bacteria to enter. However, once the tool is straightened, the little crevices disappear, making traditional reamers extremely difficult and expensive to clean and sterilise. While hospitals try to ensure sterile operating conditions, there is a slight risk that bacteria and bodily fluids from one patient stay on the instrument, and that they may be transferred to the next patient, possibly leading to cross-contamination.
Single-piece precision
The researchers and SMEs on the CLEANTOOLS project picked up where the traditional technology had left off. “We wanted to create a reamer with a flexible shaft in the middle, but made of one single piece,” explains Rainer Siring, managing director at German surgical tool supplier SIMEX Medizintechnik. That way, dirt, bacteria and blood would have nowhere to cling to.
For the shaft of their innovative reamer, the project partners used shape-memory nitinol, a metal alloy of nickel and titanium that remembers its original shape. It is flexible enough to follow the curve of the bone, but will straighten when it is exposed to heat during steam pressure sterilisation.
However, nitinol is too soft to cut into bone marrow, so a cutting tip and an end element made of stainless steel are needed. To join these two materials without mechanical joints or coupling, which would again create little nooks for bacteria, CLEANTOOLS developed a novel rotary friction welding method.
Spinning into gear
Rotary friction welding does not require melting – the materials remain solid. Two cylindrical bars are positioned in one line. One of the bars then starts rotating at high speed, while their tips are brought together with a certain amount of pressure and for a certain length of time. The two materials eventually come together, as if they were made from one piece.
Once they had found the winning combination of materials and method, the CLEANTOOLS partners created a prototype reamer that they tested with success. But Siring expects that they will have to put in another one or two years before the tool is market-ready.
“We have to manufacture the reamer in different sizes and maybe different lengths, since bones differ in length and diameter, obviously,” says Siring. “Some people are tall, others are short – and there has to be a tool to fit everyone. “The project team is working with potential business partners to find cost-effective production options. At the same time, they are looking for licensees interested in manufacturing such products themselves or having them manufactured for them.
Last but not least, their new tool has to meet the regulatory requirements laid down for medical devices. “That alone can take between 6 and 12 months,” Siring points out. “Among other things, we have to do clinical trials, which can be quite difficult and expensive. Therefore, it is possible that we have to wait even a little longer for commercialisation.” But despite the lengthy approval process, the reamer should be market-ready within a maximum of two years.