Boring buildings be gone
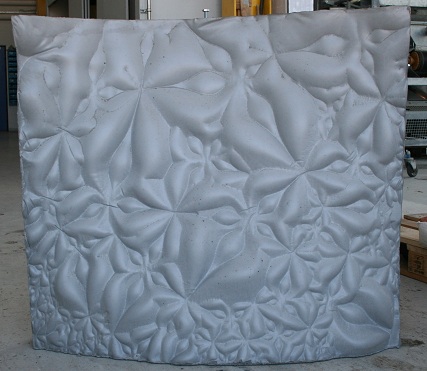
Related topics
Innovation Leadership in enabling and industrial technologies Advanced manufacturing & processing Belgium Czechia Denmark Germany Spain Sweden Switzerland Turkeydate: 16/06/2014
Project: New industrial technologies for tailor-m...
acronym: TAILORCRETE
See also: CORDIS
Contact: Contact
The EU-funded project TailorCrete aimed to narrow the difference. TailorCrete set out to develop an industrial process for creating curved concrete shapes at low cost. That would mean structures of greater appeal. To do this, the project had to study robots, special kinds of concrete and new types of reinforcement. The consortium also aimed to create new design and production tools.
TailorCrete's four years of research yielded a new process. An architect starts by designing a structure using TailorCrete's 3D design tool. Normal concrete uses moulds of styrofoam or plywood, called formwork, which results in the familiar blocky shapes.
The TailorCrete process still uses formwork, but the surface is instead cut with an on-site industrial robot. This method enables intricate shapes and smooth textures. After the formwork is cut, the robot then bends steel reinforcing to fit the available space, according to the digital design. The robots make the new process affordable and relatively simple.
Tailored concrete
Not just any concrete would go into the formwork space. "A special self-compacting concrete would first be designed, by adjusting the mix of ingredients to get the best flow properties," says Dr Mette Glavind, Vice President of the Danish Technological Institute, and project leader.
Normal concrete might not fill the space completely, leaving voids. However, self-compacting concrete's greater fluidity means it automatically fills any given space, without needing an additional process. "Furthermore, it makes it possible to cast complicated formwork and geometry, helping to express the architect's vision," says Glavind.
While TailorCrete didn't invent self-compacting concrete, it did develop all other system components. The project's main achievements include three types of formwork. One, suitable for low-medium curvature slabs, has been demonstrated at full scale and is now commercially available. The other types, both suitable for any curvature, have either been demonstrated in prototype or are ready for market.
TailorCrete's robotic fabrication process for bending and securing the reinforcement has been demonstrated at full scale, and the project is working to establish a spin-off company. The consortium can also take credit for developing software design tools covering all elements of design, including architecture, formwork and reinforcement. Testing the fully functional prototypes is almost complete.
All the project's component achievements have been drawn together in a final demonstrator – a futuristic structure in Denmark, to be completed in March 2014.
The next phase for TailorCrete will involve taking the mature technologies to the market. Individual project partners will be responsible for marketing specific technologies. Additionally, Spanish contracting company Dragados will be using the TailorCrete integrated system to create unique concrete structures.
"The financial crisis certainly didn't aid the implementation of new technology in the building and construction sector," says Glavind. "However, it seems that the market's improving. Thus our market potential is huge."