Lighter, tougher materials for large fuel savings
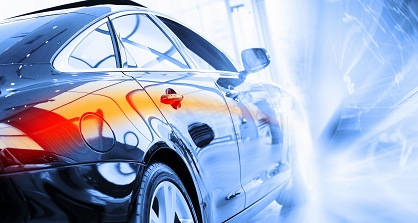
date: 27/05/2014
Project: Nanostructured toughened hybrid nanocomp...
acronym: NANOTOUGH
See also: CORDIS
Contact: www.nanotough.aau.dk
The European Union (EU)-funded NANOTOUGH project created and optimised a new range of polymeric materials, leading to their demonstration in a series of applications. The new materials could be used as alternatives to heavier and more expensive conventional metals. In particular, the project team produced prototypes such as an automotive bumper, which uses the new hybrid nano-reinforced materials and weighs only 40% of a conventional bumper.
The advantages are clear. “If we can achieve a saving of 100kg in a car, we can reduce fuel by 5 to 15%. It is very attractive to introduce lighter materials,” explains the project coordinator, Prof Jesper de Claville Christiansen from the Aalborg University, Denmark.
The composite materials must also offer sufficient strength, stiffness and toughness. According to Prof Christiansen, before the start of the project composite materials were not shown to be tough enough. However, the project team was able to replace a steel bumper beam with a nanocomposite one that could fulfil the same requirements – i.e. absorb the same impact –but with 40% of the weight. It was also cheaper to produce the nanocomposite bumper beam.
The nanocomposite materials also demonstrated improved stiffness and strength properties. Moreover, useful knowledge was gained during the project. State-of-the-art techniques were used to develop and refine materials that can be applied in products and vehicles where metals and plastics are currently commonly used.
The project benefitted from drawing on the experiences of a wide range of international partners. “If you work nationally, you do not achieve this synergy between very different environments. And certainly in the NANOTOUGH project, if it was not for the different partners participating, we would not have had the same results,” says Prof Christiansen.
One particular application investigated by the project team was in the field of aeronautics where weight is a critical issue. “The big question in aerospace is ‘can you get your craft up into space or can’t you’ – too heavy and it won’t reach lift off (or it will take off, but you can only transport a little number of astronauts or amount of fuel for the space station),” comments Prof Christiansen.
The Italian company Aviospace, one of the partners involved in the project, is carrying out further tests in order to qualify the new materials for the aerospace industry. “For instance, Aviospace carried out special fire tests to analyse where the new materials could be used in the space station,” says Prof Christiansen.
The areas in which the new materials could be used are “numerous”, emphasises Prof Christiansen, but electronic goods could be a particularly beneficial area. “Mobile phones can be dropped on the floor; so they need to be tough to withstand it, but also strong so they do not bend and damage the electronics inside. Similarly, laptops and PCs require a certain stiffness to protect the screen. All products in daily life [could potentially use nanomaterials], where it is not just a question of strength and stiffness, but where we would also like the product to withstand impact,” concludes Prof Christiansen.