A big leap forward for Europe’s footwear industry
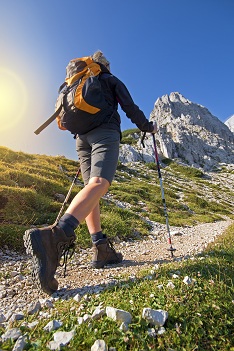
Related topics
Innovation Advanced manufacturing & processing Belgium France Italy Portugal Spain Switzerlanddate: 04/04/2014
Project: Framework of integrated technologies for...
acronym: FIT4U
See also: CORDIS
Contact: http://www.fit4u.eu/
The EU-funded FIT4U project, completed in June 2012, sought to respond to a growing demand for safety-oriented footwear – and accessories such as gloves – by developing new ways to tailor items to wearers.
The project has resulted in an integrated production chain – from software that collects data about users, to design and production – that is aimed at helping manufacturers develop and make fully personalised shoes and gloves in a cost-effective manner. The technology has been validated and assessed on pilot production lines, and is ready to be rolled out.
“The end result is personalised and comfortable safety and outdoor shoes, suitable for both workers and consumers,” explains project coordinator Dr Emanuele Carpanzano of Italy’s National Research Council. “Furthermore, the companies that participated in this project now stand to benefit through increased business from new market opportunities.”
The perfect fit
The FIT4U team developed a number of the innovative tools with users in mind. These include a biomechanical sensor capable of assessing a person’s specific footwear needs.
When the software is combined with a wearable device capable of imitating the sensation of trying on a shoe – a kind of virtual reality shoe – shoppers are given a much clearer idea of the type that best suits their needs, explains Dr Carpanzano.
The software asseses the way the foot works – and the various pressure points on it – while standing, walking or running for example. It then calculates the shape and support needed for those specific activies.
Other results include the development of profiling software using information collected from a database and from a network of the project’s biomechanical sensors. This information could be used to help manufacturers design footwear based on a market assesment of users’ needs.
The FIT4U team also developed software for automatically adapting shoe and glove designs based on this input.
Another breakthrough is FIT4U’s low-cost machine for producing shoe lasts – foot models used for manufacturing personalised shoes.
FIT4U also developed new textiles – again within a low-cost range – suitable for the upper section of shoes and able to provide greater performance for safety and sport footwear, says Dr Carpanzano.
“Cooperation and knowledge sharing among partners all around Europe would not have been possible without this EU-funded project,” he concludes. “Furthermore, new knowledge has been generated that will revolutionise production processes, materials and products, and open up new market opportunities.”