Using specialty coatings to extend the life of factory tools
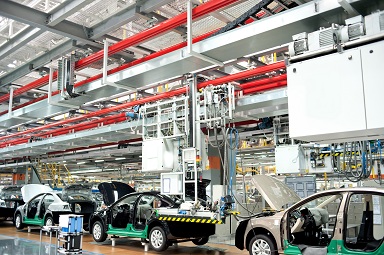
Related topics
Industrial Technologies Innovation Advanced materials Austria France Germany Italy Poland Slovenia Switzerland Ukrainedate: 27/03/2014
Project: Development of wear resistant coatings b...
acronym: APPLICMA
See also: CORDIS
Contact: www.applicma.eu
The project team experimented with layering factory tools with metallic compounds, which is expected to reduce the friction that can damage tools and make them less precise.
“Factory tools are incredibly finely-tuned pieces of equipment that produce high-precision parts. Over time, they can be deformed by friction and heat, which means the parts they produce will also be deformed,” says AppliCMA project coordinator Andreas Merstallinger of Austria-based Aerospace & Advanced Composites. “What we accomplished is a new way to coat these tools in order to tackle these problems,” he adds.
“These coatings can reduce friction and heat,” Merstallinger explains, “as well as the force needed to cut and shape raw materials into parts.” This can lower energy use and thus reduce manufacturing costs. These savings can provide benefits for many industries, especially the aerospace industry.
One of the materials that the AppliCMA team experimented with is known as AlMgB14. Though nearly as hard as diamond, the material is more slippery than Teflon. In addition, compared to diamond, the material is less costly and reacts less with steel, which means it is more durable. Given ongoing pressure to lower costs and enhance durability in factories, the potential use of such low-friction coatings in industry is unlimited.
“The process of making these coatings stick onto factory tools is very tricky. But we were motivated by the savings this could bring to a wide range of industries,” comments Merstallinger. “By the end of the project, we were able to improve the way coatings can be applied to tools,” he adds.
In one case, according to Merstallinger, the researchers were the first to successfully apply a certain type of coating made of aluminum, copper, iron and boron. Furthermore, the project team developed methods to apply materials previously considered too brittle to be used as coatings.
Many types of factory tools are used to make parts and components, including those that drill, cut, stamp, and inject raw materials into moulds. “In particular,” says Merstallinger, “coatings can help maintain the shape of punching tools, which means they can produce parts more accurately.” Such coatings can also be used on airplane and spacecraft parts that must withstand high levels of heat and pressure.
AppliCMA project partners included universities, research and development firms, industrial companies, tool manufacturers, as well as aerospace and nanotechnology companies. It is expected that the project’s achievements will lead to further technological breakthroughs and additional benefits for companies and researchers internationally.