Fitted, fast and high-tech: a new generation of surgical implants
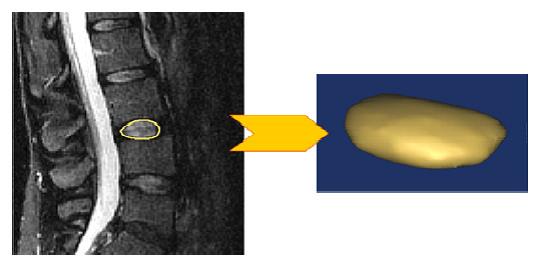
Related topics
Health SMEs Innovation in SMEs Health, Demographic Change and Wellbeing Advanced materials Belgium Germany Netherlands Poland Spain United Kingdom Switzerlanddate: 05/02/2014
Project: SME Supply Chain Integration for Enhance...
acronym: CUSTOM-IMD
See also: CORDIS
Contact: http://www.ascamm.com/en
Dental and medical implants can be essential to recovering the normal functioning damaged teeth and bones. However, traditional implants often fit imperfectly or use materials that are not fully compatible with the body, which can cause post-surgery complications. In addition, patients often have long waiting times for implants, prolonging discomfort before treatment.
Inspired by rapid manufacturing processes used for industrial prototypes, researchers at the EU-funded project Custom-IMD looked at how to overcome these problems. Coordinator Dr Esther Hurtos from ASCAMM in Spain says: “We were trying to develop a process with improved materials and a better fit for the patient.”
Pooling their expertise, the group developed materials, software and procedures for building custom-made, biocompatible prosthetics using small-scale manufacturing techniques. Because the process integrates imaging, design and manufacture, it can build a safe, strong implant within 48 hours of receiving an order.
This system uses 3D images of the body to calculate the exact shape and size of the implant the patient needs. It then builds the new part by laser sintering – a process in which lasers are guided by an image to add layers of powdered material on top of each other where needed until the exact shape required is achieved.
Efficiency by design
The new technology reduces waiting times and post-surgery complications, saving on care costs and helping patients resume their normal lives more quickly. The faster surgery and shorter hospitalisation times also reduce the impact on patients’ lives.
Manufacturing costs are reduced, too. Dr Hurtos says that the main impact on implant production costs is the process automation and use of materials. In the new process, “you only use the right amount you need to build the part,” she says.
Overall, the more efficient process could save up to 20 % of the cost of using traditional implants in Europe. The only new costs for hospitals are for the materials. Access to the software for the process is simple, Dr Hurtos says.
“You just need internet access to an online platform where algorithms anonymise the medical images for confidentiality,” she says.
Innovative polymers and ceramics and novel image-processing software from the project are already being commercialised. Several of the companies involved in the project have taken out patents on their results, while breakthroughs in automatic manufacturing are expected to benefit other industries.
In healthcare, implant manufacturing machines, cranial implants and fully ceramic dental implants are now commercially available. Dr Hurtos says this is also the first step towards new types of spinal implant and customised alternatives to titanium implants for broken bones, although new applications need to pass strict medical device regulations for implant suppliers.
The collaboration between 22 very diverse specialist institutions from six different countries brought a unique solution to cost, design and manufacturing problems in prosthetics manufacture. Links from the project are going strong in new work on tailoring cell responses for the body to repair its own tissues.
Dr Hurtos says: “The team finished the project with a feeling of it having been worthwhile … the project would have been impossible without the EU’s contribution.”