“3D printing” holds potential to transform how objects are manufactured
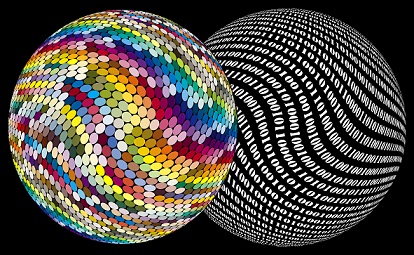
date: 28/01/2014
Project: Support Action for Standardisation in Ad...
acronym: SASAM
See also: CORDIS
Contact: www.sasam.eu
Feenstra, of the Netherlands-based research organisation TNO, heads a team that is developing a roadmap to standardise how additive manufacturing – better known as “AM” – can be incorporated into mainstream manufacturing facilities and processes. Standardisation is mandatory for any technology being implemented into industrial production.
Rather than firing streams of ink onto a page, “3D printers” eject binders onto finely powdered steel, plastic or other materials to bind them together. The process literally builds up three-dimensional objects – even intricate aerospace parts – layer-by-layer. This type of additive manufacturing starts from nothing and positions and binds raw materials where the part eventually will be. It is the opposite of traditional “subtractive” manufacturing, in which a block of material is carved away until the part appears.
The concept has the potential to revolutionise how both high-tech parts and everyday objects come to be. Making a children’s toy or a part of a shoe, for instance, can be accomplished by “drawing in plastic or metal.” Some high-tech parts have already clearly demonstrated the merits of the technology.
“The idea has been around since the 1980s, but originally only to make prototypes of objects. The technology was marginal for a long time,” explains Feenstra. “It has emerged in the past five years and is really soaring now.”
Traditional manufacturing typically involves casting liquefied metals, plastics or resins into a mould, or cutting or forming parts from large pieces of raw materials. Before anything can be made, moulds or dies have to be designed and produced, which can consume a significant portion of manufacturing time and cost. In addition, raw materials are often wasted along the production cycle.
AM, or 3D printing, eliminates these problems. “With additive manufacturing, you have a big bag of powdered metal or plastic – and you only use as much as you need,” says Feenstra. “Nothing gets thrown away.”
With AM, the first step is to make a three-dimensional model of the object with computer-aided design (CAD) software. The computer is connected to a device equipped with the materials needed to make the object: powdered metal or plastic, glue, resin or whatever the ingredients might be. The device acts like a printer, with “printheads” not dissimilar to those in a desktop printer that spray binder material onto a flat surface, where the materials are solidified one horizontal layer at a time.
Connected to conveyor belts and suspended above the surface, the printheads repeatedly sweep over the surface one side to the other, slowly but steadily building up the object according to the three-dimensional model on the computer. If a ceramic coffee cup was designed on the computer, for example, then the 3D printer would make the cup – from the base to the rim – one super-thin layer after the next until it is complete.
AM devices are being used in a wide range of industries, including aerospace, automotive, medical, dental, consumer products, electronics – even sports and fashion. 3D printers have been used to make surgical implants, artificial fingers, aeroplane and car parts, jewellery, costumes for action films, and components of sports shoes. Prosthetic ears and noses have been made, and it is envisioned that in the future artificial organs could be produced and transplanted into people.
“It is not magic,” says Feenstra. “A 3D printer can only make an object if it first has been properly designed on a computer and if the device has all the ingredients available to build up the layers,” he adds.
“The only thing lacking now for industrial implementation is an official standardisation of the processes and parts,” says Feenstra. “After we come up with a consistent set of quality labels, and ways to check and trace the parts being produced with AM, the technology will spread very quickly. There is a serious industry behind it.”
Estimated at US $1.7 billion in 2011, the global AM market is predicted to reach US $3.7 billion by 2015. There are currently 30,000 plastic and 500 metal AM machines in operation.
Related article: What does the future hold for 3D printing?