On to second-generation bioethanol
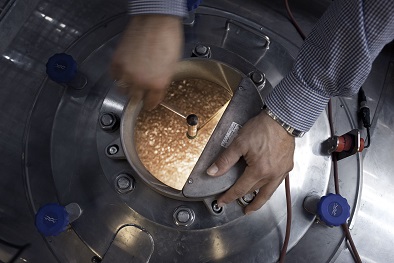
date: 18/09/2015
Project: Integration of Biology and Engineering i...
acronym: PROETHANOL2G
See also: CORDIS
By substituting fossil fuels in transport, power generation, the chemical industry and elsewhere, bioethanol could contribute substantially to the EU achieving its greenhouse gas emission (GHG) reduction goals. The sector has been growing continuously over recent years. Today, Europe boasts about 8.8 billion litres of installed production capacity with a market value of close to €8 billion, which only the US and Brazil exceed.
Most bioethanol production takes place in first-generation (1G) plants, which process crops such as wheat or maize, leading to possible competition between food and energy needs. Advanced second-generation (2G) bioethanol production from lignocellulosic biomass, i.e. waste plant matter from forestry or agriculture such as wheat straw or sugarcane bagasse, could change that and substantially increase the GHG reduction potential at the same time.
“Our approach to bioethanol production can reduce GHG emissions by up to 90%, while the conventional crop-based technology achieves a reduction rate of 30 to 50%, depending on the efficiency of the plant,” says Francisco Gírio from the Portuguese National Laboratory for Energy and Geology (LNEG). He coordinated the PROETHANOL2G project, a collaborative effort between partners from Europe and Brazil.
From waste to fuel
When the PROETHANOL2G project started in 2010, no commercial advanced bioethanol plant existed in Europe. Today, Europe’s first plant is up and running in Italy. Nonetheless, considerable R&D will still be needed to make 2G bioethanol a true alternative to its crop-based cousin.
“The main challenge is mostly due to the heterogeneity and complex chemical structure of lignocellulosic biomass,” Gírio explains. “This means that you have different molecules in the raw material compared to crop-based biomass. Therefore, it requires a very effective pre-treatment technology as well as a very good recombinant yeast strain for fast and easy conversion of all sugars after the biomass pre-treatment.”
The production process involves several steps – from pre-treatment and enzymatic hydrolysis to break down the molecules into sugars, to fermentation of the sugar solution with the help of yeast and distillation.
Major advances
As one of its main achievements, the PROETHANOL2G team developed a novel recombinant yeast strain which enables efficient fermentation of different sugars, thus lowering the production costs of advanced biofuels from waste biomass.
In addition, the project vastly improved the integration between biomass pre-treatment, enzymatic hydrolysis and fermentation, which is seen as a challenge to making this advanced biofuels technology competitive. The team also came up with a novel distillation system, which reduces energy consumption and enables the recovery of the largest part of the enzymes. Since one of the main costs of the 2G technology is the cost of the enzymes, being able to reuse them back in the hydrolysis represents major progress.
For the Brazilian market, the consortium altered the PROETHANOL2G process slightly, as a stand-alone 2G set-up might be less feasible in a country such as Brazil, with such large 1G usage.
“Therefore, we integrated our European 2G technology in the 1G technology in Brazil,” says Gírio. This combined 1G-2G system may be the secret to making the PROETHANOL2G technology a success in the South American country, where Inbicon A/S, an industrial project partner from Denmark, is in contact with a major industrial player, planning a joint venture to deploy a commercial 1G-2G plant.