A tunnel yields a whole lot of valuable materials
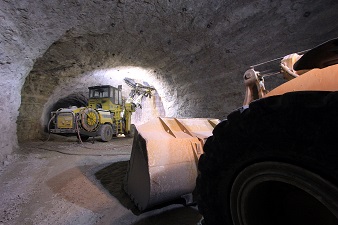
Related topics
Environment & climate action Innovation Austria France Germany United Kingdom Switzerland Environmentdate: 02/07/2015
Project: Development of Resource-efficient and Ad...
acronym: DRAGON
See also: CORDIS
Boring a tunnel through a mountain for a railway, or beneath a city for a metro, leads to many tonnes of excavated material. Tunnelling companies have to dispose of this muck – as the excavated soil and rock is called by industry – in landfills as waste or for use in land reclamation.
That’s a lot of valuable minerals and building materials going to waste. Industry’s challenge has been to efficiently recover the usable from the muck. The EU-funded project DRAGON has developed an automated system to analyse and sort excavated material as it is removed from the tunnel face by boring machines.
The system could provide a stream of competitively priced materials for a range of industries, as well as new revenues for tunnelling companies. The system’s units can be integrated into the large machines normally used for boring tunnels.
All materials are sorted and processed underground as soon as they are removed from the boring wall. From there the materials can be transported out of the tunnel to be sold to industry, while the rest goes to waste.
“These breakthrough technologies will help Europe’s tunnelling and underground construction industry to become more competitive,” says project coordinator Robert Galler of Montanuniversität Leoben in Austria. “They would also substantially reduce environmental pollution, CO2 emissions and land use by greatly reducing waste from underground construction.”
How it works: from x-rays to microwave technologies
Ongoing and planned tunnels in Europe are expected to result in around 800 million tonnes of excavated material. DRAGON’s technology could be used to help excavation companies earn an additional estimated €150 million a year from this material, says Galler.
DRAGON developed prototypes of advanced photo-optical, x-ray and microwave technologies that can be used directly behind the cutting head of a tunnel boring machine. The units analyse the stream of excavated rock and earth, providing information such as size, shape and mineral and water content in real time. An underground plant then sorts the material based on the test results.
“This novel approach maximises the use of excavated material from underground infrastructure projects,” Galler explains. “The sorted material can be used on site as aggregates for constructing tunnel walls or can be sold to other sectors such as the cement, steel, ceramic or glass industries.”
He cites the example of the ongoing excavation of the Koralm rail tunnel in Austria. Two tunnels, each about 10 metres in diameter, are being bored underground over a distance of about 33 kilometres as part of a rail line between Graz and Klagenfurt.
The excavated granite gneisses are “good construction materials” of a better quality than available from most quarries, says Galler. “Yet we treat this material as waste,” he adds. “That has to be changed.”
Prototype test
After lab tests, DRAGON trialled some of its sorting system’s prototype components at a factory belonging to project partner Herrenknecht in Germany. A component to monitor excavated material was tested at the Bossler rail tunnel, which is being built between Wendlingen and Ulm in Germany.
The prototype test used two conveyor belts to sort three different types of materials. The test found quartz that could be used to make glass, limestone for steel production and material for making concrete. The system could be expanded to sort five different types of materials, adds Galler.
DRAGON has held demonstrations of the technology at various conferences, including the World Tunnelling Congress at Dubrovnik, Croatia in May 2015. Other demonstrations are planned in Austria (Leoben and Salzburg) and France (Lyon). At such events, project partners also discuss the legal changes needed before DRAGON’s technologies could be used in tunnelling operations.
For example, Galler says the EU needs a common law allowing industry to sell and use the materials recovered from excavating underground structures. Under current waste legislation, they are not able to process the muck they take out of tunnels to easily create mineral products; most of it must instead be sent to landfill.
Interest in the technology is high. The project has been invited by the authorities in France to make a presentation on how the technology could be used to recover materials during the construction of about 160 km of new metro lines in areas surrounding Paris.
In the UK, DRAGON has been asked to present the technology for possible use during tunnelling operations for a proposed rail line between London and Manchester.