Setting the injection moulding world abuzz
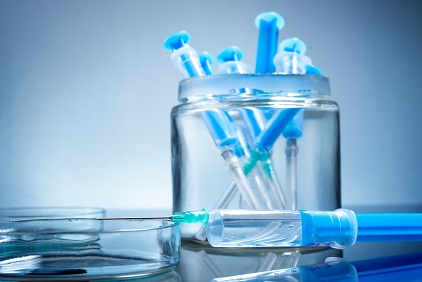
Related topics
Innovation SMEs Industrial Leadership Innovation in SMEs France Netherlands Spain Nanotechnologies, advanced materials, advanced manufacturing & processing, and biotechnologydate: 09/04/2015
Project: Machine for Microparts Moulding based on...
acronym: SONO”R”US
See also: CORDIS
The biggest breakthrough lies in the way the machine developed by the SONO”R”US project melts the material, in this case plastic. Conventional injection moulding involves heating up plastic pellets in a syringe-like contraption with the help of electrical heaters until they become viscous. This viscous plastic mass is then injected into a mould.
This process, however, can be inefficient when it comes to producing mini- or micro-sized plastic parts. The problem: conventional systems heat up larger quantities than needed for an individual part.
“Imagine – with the syringe in mind – that you need to apply a very small quantity of plastic,” says Enric Sirera of Ultrasion, the Spanish company now commercialising the SONO”R”US 1G ultrasonic moulding machine (it was developed in collaboration with three SMEs – Mateu y Solé (the machine producer), Promolding and Cedrat – and Ascamm industrial technology centre). “The syringe is full of material, which has been sitting at a high temperature for a long time. The smaller the part, the smaller the drop you need to apply and the longer the material will have to sit in the syringe.”
Many of these materials – especially those for medical applications – will degrade if exposed to high temperatures for long periods of time. In addition, using the traditional heating method, they will still be quite viscous. Therefore, injecting them into the mould requires considerable force, basically degrading the material even further.
Innovation taking shape
Building on the achievements of its precursor SONOPLAST, the SONO”R”US project took this project’s approach further: starting from the solid plastic, the machine only melts the tiny quantity needed for the individual part – up to 1.5 g – exclusively applying ultrasonic energy.
“It is like with cold hands: if you start rubbing them together slowly and softly, your hands will only get a little warmer,” Sirera explains. “However, if you start going faster and applying pressure, they will warm up quickly. When we apply ultrasonic energy to the pellets, it drastically reduces the plastic's viscosity. All in all, that means you only heat up whatever you need and it is also much more liquid, so that you need less pressure and effort to mould it into the mould cavities.”
Huge progress for tiny parts
As a result, power consumption is up to 90 times lower than in the case of conventional injection moulding processes. What is more, the risk of degradation is reduced considerably thanks to the “only heat what you dose” approach and the use of ultrasonic energy, making the method particularly suitable for producing tiny medical devices such as aneurysm clips, valves or catheters.
But there are countless other areas of application, such as in precision mechanics, aerospace, optics l and electronics.
The SONO'R'US technology has been on the market since the beginning of 2013 and has created quite the buzz on an international level. So far, Ultrasion has sold 12 machines to clients all over Europe and in the USA. Due to the technology's characteristics, it has been a hit with medical device manufacturers. Currently, Ultrasion is validating the technology for several electronics manufacturers, so business is looking up, says Sirera.