A safer, cheaper, greener Li-ion for electric cars
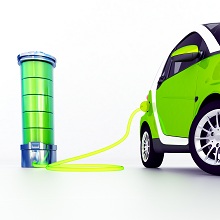
Related topics
Innovation Transport Smart, green and integrated transport Austria France Germany Ireland Italy Spain United Kingdom Switzerland Nanotechnologies, advanced materials, advanced manufacturing & processing, and biotechnologydate: 27/02/2015
Project: Lithium-Air Batteries with split Oxygen ...
acronym: GREENLION
See also: CORDIS
Lithium-ion (Li-ion) rechargeable batteries have sparked the attention of electric vehicle manufacturers ever since they first came on the market in the early 1990s. Among their advantages are a shorter charge-time and a higher energy-storage capacity than other types of rechargeables, such as nickel-metal hydride batteries.
Powering a car longer between charges gives Li-ion batteries a competitive edge, but manufacturers still need to overcome some barriers to their wider use. Current Li-ion battery technology can short-circuit, while faults in materials can lead to the occasional fire – blamed for millions of laptop and smartphone battery recalls over the years, and even the grounding of Boeing 787s in early 2013. Li-ions are also relatively more expensive to make.
The EU-funded project GREENLION is addressing these barriers with new components, chemical technologies and manufacturing processes to produce cheaper, more-dependable and greener Li-ion batteries for electric cars.
Among the breakthroughs: the project has tested new types of battery electrodes with promising results, created a compact, modular design for powering vehicles, and developed cheaper manufacturing processes.
These breakthroughs also have the potential to help manufacturers become greener, cut assembly time and make it easier to recycle parts when the battery is no longer usable, says project coordinator Iosu Cendoya of Spain’s Fundacion CIDETEC.
The innovations, including component development and the automation of manufacturing processes, would cut costs by 15% for a whole battery pack, he adds.
“Altogether, these improvements will allow higher energy efficiency and substantial cost reductions, thus ensuring real competitiveness for lithium-ion batteries based on new technologies,” says Cendoya.
Next-generation Li-ions
Batteries are made of two electrodes (an anode and a cathode), separated by an electrolyte. Typical Li-ion anodes are made of graphite, while the cathodes use lithium cobalt oxide. A solution of lithium salts and organic solvents is used for electrolyte.
GREENLION, which ends in October 2015, is on schedule to develop a range of environmentally friendly innovations that reduce the cost and manufacturing time for these units (cells) and put them together as battery packs for electric vehicles, says Cendoya.
The project developed a new modular design to reduce weight and make heat management more efficient. Self-managing units or modules can be put together more easily, efficiently and for less cost, he adds.
“This module is seen as a simple and reliable building block to simplify and reduce the cost of manufacturing whole battery packs, with the lowest possible environmental impact,” says Cendoya. The innovations include:
- more environmentally friendly battery materials that reduce chemical use;
- innovative processes (the use of aqueous slurries for electrode manufacturing) – to reduce electrode production costs and environmental pollution;
- new assembly procedures (including the use of laser cutting and high temperature pre-treatment) – to reduce the time and cost of cell fabrication;
- an automated module and battery pack assembly line for increased production output and reduced cost;
- lighter battery modules designed for easy assembly and disassembly for recycling battery components;
- waste reduction – the modular design and use of new materials allows recyclers to safely recover active and inactive battery materials.
“These new automated processes will contribute to a substantial cost reduction of lithium battery packs, and will open them up to mass production,” says Cendoya. “Automation and the new manufacturing processes will improve the quality and yield of the production, while at same time reducing labour costs.”
The researchers scaled up and tested these innovations on pilot manufacturing lines at project partners Imerys (Timcal), WIFAG-Polytype Technologies, Manz Italy, Cegasa Internacional and Mondragon Assembly. Project partners Volkswagen and SEAT will assess the final assembled battery module to see whether it meets the specifications required for electric vehicles.
“The wide deployment of lithium-ion batteries by the automotive industry would boost Europe’s battery market and would further strengthen the central role of these systems in other industries for energy storage,” he adds.
Below photos of GREENLION cells and module prototype
©IK4-CIDETEC