A big step forward for electronics
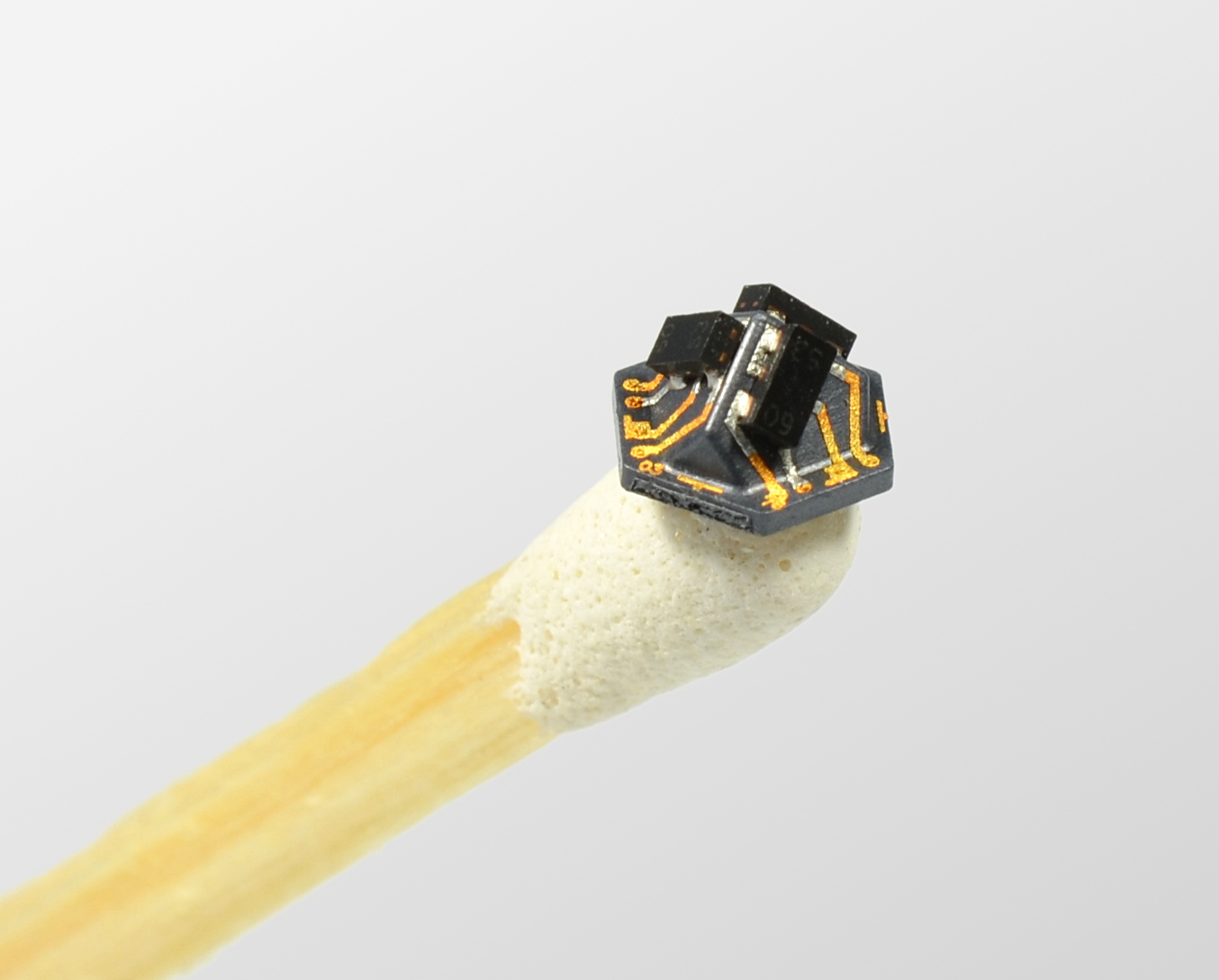
Related topics
Innovation Innovation in SMEs Advanced manufacturing & processing France Germany United Kingdom Switzerlanddate: 03/11/2014
Project: Pilot Factory for 3D High Precision MID ...
acronym: 3D-HIPMAS
See also: CORDIS
Contact: Contact
Update on 3D-HiPMAS , December 2015
The commercial venture based in France, S2P, opens the way for European companies to produce ever smaller, cheaper and smarter electronic devices.
S2P launched in November 2014 and currently has five staff working mostly on design studies and development. They provide advice to electronics manufacturers on how to use 3D-HiPMAS’s new technology. This combines plastics moulding, 3D laser direct structuring and metal deposition techniques for applying electronic circuit tracks on 3D plastic devices, so called Moulded Interconnect Devices (MID). The 3D-HiPMAS process would halve the size of the tracks – a breakthrough in miniaturisation.
“Producing metal tracks with very small size was a critical point in order to access new markets for this spin off,” says 3D-HiPMAS project coordinator Wolfgang Eberhardt of Hahn-Schickard. “The creation of S2P was only made possible thanks to 3D-HiPMAS.”
In 2015 the company plans to propose ways to develop products and perform trials of the manufacturing process on a pilot line being developed in France.
The pilot line will be similar to the one set up by 3D-HiPMAS at Hahn-Schickard in Stuttgart, which includes new equipment and technologies developed by the project. Micro-electronics SMEs and other companies can use it to develop prototype components and produce samples.
3D-HiPMAS also developed three new thermoplastic materials suited to the laser direct structuring process pioneered by the project. One of them targets applications in medical technology. Another – available as two types of material with improved thermal conductivity – would enable new applications, especially in lighting technology, Eberhardt says.
The third is a liquid crystal polymer suited to the project’s manufacturing process. All are currently available on the market through one of the project’s commercial partners.
Eberhardt expects the project’s equipment, processes and plastics to be applied in e.g. the energy, medical, communication and transport sectors. The new market opportunities include:
- fuel cell applications – prospects encompass uninterruptable power supply (UPS), electrical tools, generators and for small vehicles;
- medical – can reduce the size of devices such as hearing aids and new sensor components with higher performance and stability;
- telecommunication – enables increased performance at reduced size for components such as micro switches;
- automotive – allows the integration of sensor functionality directly on an existing design, such as for a quick connector on a coupling system, or for miniaturisation of pressure sensors or strain gauges.
At the end of the project, the team held a contest for new MID ideas from outside the project. The winner will be able to try the project’s technology by having a proposed product made at the pilot factory.
Text from 2014
Smarter is better for systems manufacturers
In the race for new markets, electronics manufacturers have to produce ever smarter and more streamlined devices. An EU-funded project helps companies achieve this more cheaply and with less waste – a boost to their competitiveness.
The trend towards smaller, smarter devices is pushing electronics manufacturers to use streamlined components that integrate electronic circuitry directly onto plastic parts (moulded interconnected devices – MIDs). The EU-funded 3D-HiPMAS project has found solutions to several technical problems to help European manufacturers take full advantage of this trend.
The project team predict that the technology could save up to 50% or more of current production costs through labour, materials and energy savings, with more as it develops further. By helping small to medium-sized enterprises (SMEs) develop cheaper ways of producing new products, they hope to promote technical innovation in Europe, help small businesses grow, and create jobs.
Project coordinator Heinz Kueck of the German Institute for Micro Assembly Technology of the Hahn-Schickard-Gesellschaft e.V. says: “The 3D-HiPMAS technology uses new materials and techniques to build circuits directly onto plastic components. For a broad range of electronic systems, this saves time compared to the traditional process of making plastic parts and circuits separately then assembling them in an additional stage.”
He adds, “Electronics are scaling down all the time. The aim is to make metal lines smaller on the plastic parts so you can have more components on the device, supporting the trend towards miniaturisation.”
Three technologies make the estimated savings possible, all developed by the project:
- new plastics and plastic moulding technology combined with new laser technology and metal deposition for applying circuit tracks would halve the size of the tracks;
- new assembly technology would build 3D pieces more accurately, creating less waste from defective parts;
- new inline monitoring and inspection would allow faster, cheaper quality control during manufacturing.
To showcase its solutions, the project is developing a pilot factory to manufacture miniaturised components that meet the needs of high-tech industries such as health care, communications and energy.
The factory will include all the new technologies from the project to help micro-electronics SMEs build prototype components and small volume series in order to develop more efficient ways of producing their products. Kueck expects the factory to be ready by the end of the project in September 2015.
Industry potential
A group of seven companies outside the project is currently assessing the technology. 3D-HiPMAS has also developed four demonstrator products to test the factory and to show how the technology could work: a miniaturised controllable fuel cell, a more streamlined hearing aid, an advanced 3D micro switch and a miniaturised pressure sensor.
According to Kueck, components built with the 3D-HiPMAS technology have better mechanical performance and better, more reliable circuitry than state of the art MID circuits.
Healthcare companies are already interested in the project’s process for applying smart plastic based systems to medical devices that come into contact with human tissue and liquids, says Kueck, because the new process makes very robust circuitry.
At the same time, companies are already interested in the new laser machinery, while the project’s new heat-conducting materials are generating interest for solid-state lighting such as LED lamps, he says.
At the end of the project, the team will hold a competition for new MID ideas from outside the project. Three winners will have the chance to try the project’s technology by having their proposed products made at the pilot factory.
Kueck says, “This is a very powerful technology. It can develop new, miniaturised smart devices that are not currently possible, enhancing quality of life. The overall impact in Europe will be to introduce a high-performance, difficult-to-manufacture technology to Europe, improving its economy”.
Magnetfeldsensor
© HSG-IMAT