0.05 mm: a new accuracy standard for industrial robots
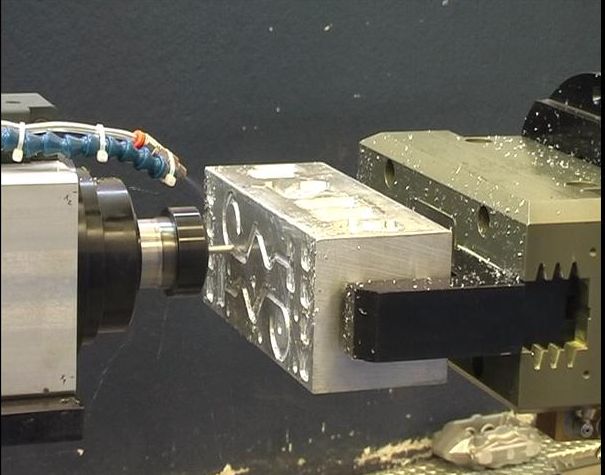
Related topics
Innovation Advanced manufacturing & processing Belgium Czechia France Germany Greece Italy Sweden United Kingdomdate: 03/11/2014
Project: Plug-and-produce COmponents and METhods ...
acronym: COMET
See also: CORDIS
Contact: Contact
To gain an edge in highly cost-competitive markets, manufacturers need robotic systems that can quickly switch between diverse machining operations, with no compromise on quality, reliability and accuracy.
Machining usually involves taking a raw material and cutting, milling, lathing or fashioning it into parts and tools for different uses – from car panels to precision medical instruments to moving parts in a paintball gun.
Robots are two to five times cheaper than traditional machine milling systems. That alone made innovative solutions developed by the EU-funded project COMET very attractive to industry in Europe.
“Milling machines are fantastic but factories really need more flexible, reliable and cost-efficient ways of building all the tools and parts that go into our aircraft, cars, machine parts,” says project coordinator Jan Willem Gunnink of UK-based Delcam.
Traditional machining is accurate to 0.001 mm, whereas robots for machining applications are still at 1 mm. COMET has managed to get robot accuracy down to 0.05 mm, which is a significant improvement on today’s machines.
“We proved with our seven tech demos that, while robots are not ready to machine an Airbus turbine blade, they are definitely viable for the pre-manufacturing processes of, for example, metal parts, moulds and dies used in many sectors.”
COMET improved the absolute positioning accuracy of industrial robots so they could quickly react to changing conditions during production. Improvements in programming and simulation software were needed to ensure “first-time-right”, adaptive machining once production commences. This results in less wastage costs and faster turnarounds between jobs.
Market-ready already
Among its many achievements, COMET has come up with an integrated programming and simulation environment (PSIR), as developed by partner Delcam, which can test and demonstrate on- and off-line software, and which draws on data, metrics, tools and programming supplied by different partners.
“Our partners have shown how joined-up thinking results in closer-to-market-ready adaptive control solutions for better industrial robots,” says Gunnink.
Team members are joining forces with other EU and national project partners to explore new applications for COMET’s robotics solutions in fields such as grinding, abrasive finishing, and laser and fluid polishing.
“The software Delcam developed under COMET is already generating up to a million euros in additional sales,” says Gunnink.
That is one of many sales streams coming out of the project’s work. Lund University, a project partner in Sweden, studied what happens when robotic arms go off course and have since created Cognibotics – a spin-off which helps factories deal with common problems like friction and backlash (a small amount of movement in the robot’s joints that reduce accuracy).
Germany’s ARTIS-MARPOSS, a project partner, used its Genior modular process monitoring system to detect broken, worn or missing tools. Process monitoring like this improves the quality, reliability and stability of the cutting process, says Dirk Euhus, MMS research manager at ARTIS. And the prototypes developed in the project widen the scope of applications.
“Market experience with our existing product – and cooperation with end-users – boosted progress during the development stages,” Euhus adds. “European aerospace manufacturers are searching for mature, flexible and cost-effective production technologies. We expect a parallel growth trend for robot manufacturing solutions, each requiring tool monitoring systems like those developed in COMET.”
Fraunhofer IPA, another partner from Germany, carried out advanced R&D on a compensation mechanism (HDCM) which has been developed by fellow project partner Nisaform into a functioning system that monitors (using the ATIR technology of partner NIKON) and measures any misalignment between programmed and real robot positions.
More details about exploitable results like this can be found on the project’s website, including training materials on using robots for machining, explanations of the adaptive tracking system worked on by Nikon Metrology, and much more.
Aim for the moon
One of the keys to COMET’s success, says Gunnink, has been to include robot integrators, like SIR and Gizelis from the start: “They told us what they needed to make the outputs as ‘tech-ready’ as possible at the end of the project, and now they benefit by having extra services to offer their clients.”
Of course, great results still need a clear commercial plan and partners who will exploit them, he stresses:
“We spent public money, so we’re prepared to fly our results to the moon and back to give taxpayers a return on investment. Delcam and our other exploitation partners are already making sure the results don’t collect dust!”