Augmented reality improves safety and productivity in mines
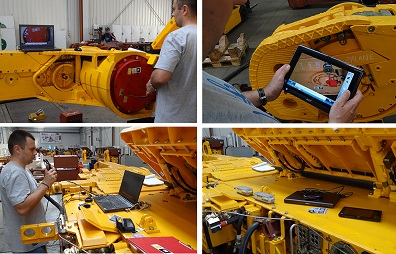
date: 26/09/2014
Project: Enhanced miner-information interaction t...
acronym: EMIMSAR
See also: AITEMIN
Contact: Contact
Miners work in confined spaces with limited visibility alongside large and dangerous machinery. The atmosphere can be dust-filled and hazardous. Much of the machinery is too large to be moved easily out of the mine. It must be maintained and repaired where it stands.
A new tool is helping miners to ‘see’ more clearly and work more quickly and safely. Using systems developed by the EU-funded project EMIMSAR, miners can view ‘augmented reality’ versions of their equipment on handheld computers and helmet-mounted displays. They can move through images of the machine and its components, call up data on the history and present condition of the machine, or be guided on how to repair or maintain components.
Sensors on the machinery provide useful insights into the wear on heavy-duty components such as gears and chains. For instance, temperatures and rates of acceleration are recorded and analysed. Sound sensors sample noise from the sprockets on mining ploughs and flexible conveyors – alterations in noise during their operation indicate their level of wear.
The sensor data is fed into a knowledge-based maintenance system, where it is combined with background data on components and libraries of machine and component visualisations. That information is combined to create information-rich, real-time visualisations of the machinery that can be viewed by the miners as they work on the machine. There are also voice-overs that provide step-by-step instructions on maintenance procedures.
The system greatly improves the productivity of the maintenance teams, says EMIMSAR’s coordinator Juan Carlos Catalina of the Asociacion Para La Investigación Y Desarrollo Industrial De Recursos Naturales in Spain. Back at the mine’s control centre, managers can combine the real-time sensor data with information on resources, staff skills and capabilities to improve maintenance planning.
The EMIMSAR system proved so successful that it has been widely deployed by mining company RAG, Germany’s largest coal mining corporation. RAG were partners in EMIMSAR and worked closely with the German engineering consultancy, DMT, and the Polish Mining Automation Institute, KOMAG, on the development of the maintenance system.
“The system is currently in use in all of RAG’s mines for maintenance planning for long wall equipment, as originally envisaged,” says Catalina. “But it is also used on belt conveyors, loaders and many other machines.”
Force sensor and positioning system
Other successful developments from the EMIMSAR project include a patented ‘pick force sensor’ that measures loads on the ‘road-header’, a boom-mounted excavator. Pick force sensors are now being built into a range of equipment by the Austrian subsidiary of the Swedish mining and construction company, Sandvik, another EMIMSAR partner.
Wireless positioning and navigation technologies were also developed. Normal radio systems work poorly in a mining environment. The EMIMSAR team came up with a simple solution. Carefully positioned fixed nodes in the mine tunnels communicate with mobile nodes worn by miners. The greater the signal intensity, the closer the miner is to a fixed node. Measuring signal intensity at two fixed nodes provides a reasonably accurate measure of the miner’s position in the tunnel.
“The navigation aids reverse the roles of the nodes: the mobile device determines its position by estimating the distance to the nearest fixed nodes. They could be very useful in emergencies such as a fire,” says Catalina. “Miners could identify and follow alternative routes to safety, even in thick smoke.”