Flight plan for innovative aircraft
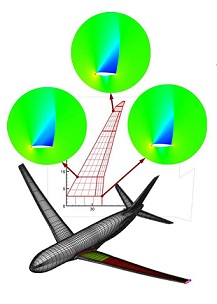
Related topics
Innovation Transport Smart, green and integrated transport Belgium France Germany Italy Netherlands United Kingdom Russian Federation South Africadate: 16/06/2014
Project: Future fast aeroelastic simulation techn...
acronym: FFAST
See also: CORDIS
Contact: http://www.bris.ac.uk/aerodynamics-...
Currently, manufacturers use relatively simple design models that can exclude complex aerodynamic behaviour, says Ann Gaitonde, a senior lecturer in aerodynamics at the University of Bristol and coordinator of the EU-funded project FFAST.
These models are then combined with the results of extensive wind tunnel tests to achieve the best design for the proposed aircraft. With multiple rounds of adjustments, the process can be costly and time consuming.
FFAST has developed more accurate simulation models, along with techniques to reduce the computational time. The more efficient techniques could result in significant cost and time savings for evaluating the aerodynamic forces on new aircraft designs, says Gaitonde.
“Detailed aerodynamic models of aircraft lower the risk of having to make design modifications at a later date and reduce the need for expensive tunnel testing,” she adds.
FFAST’s techniques also aim to speed up the evaluation of innovative designs to meet the demand for greener, more fuel-efficient aircraft – without affecting safety.
“The end-result would be an improved ability to design greener aircraft, reducing emissions,” says Dorian Jones, a senior lecturer in aerodynamics at the University of Bristol and a FFAST researcher. “The FFAST methods would also lower design costs, ensuring the competitiveness of the EU aerospace industry.”
Extreme forces in flight
For aircraft design, engineers need to consider a large range of flight conditions to ensure all the extreme forces that could affect various aircraft components are correctly identified. This analysis to identify any such problems is best done earlier in the design process.
If structural changes are found to be needed later on in the process the aerodynamic analysis needs to be repeated. For a civil aircraft under development, each cycle could require many weeks of analysis – and additional costs.
To reduce this risk, FFAST’s researchers first identified more details about flight conditions and obtained more accurate information about the maximum loads that could be put on aircraft structures. This is coupled with the more efficient algorithms developed in FFAST to reduce the time needed to process the additional details.
The feasibility of these techniques – including the new algorithms was evaluated on computational test cases, including models of a full aircraft.
The team found that a combination of FFAST techniques with current technologies could reduce the time needed for the average design process by more than 90 %.
These techniques also allow aircraft engineers to experiment more with designs at the conceptual stage – since the risk of failure is reduced – opening the door for innovation, says Gaitonde.
More investment will be needed to further develop the project’s techniques for commercial use. This would include creating the initial software for assessing designs.
Many of the project’s partners – including Airbus, Europe’s largest aircraft manufacturer – have made follow-up proposals for EU and national funding to build on FFAST’s research.
The project’s work has sparked interest from other industries, says Jones. Wind turbines for generating electricity need similar tests to ensure they can handle wind gusts, for example.