EU tooling industry tools up
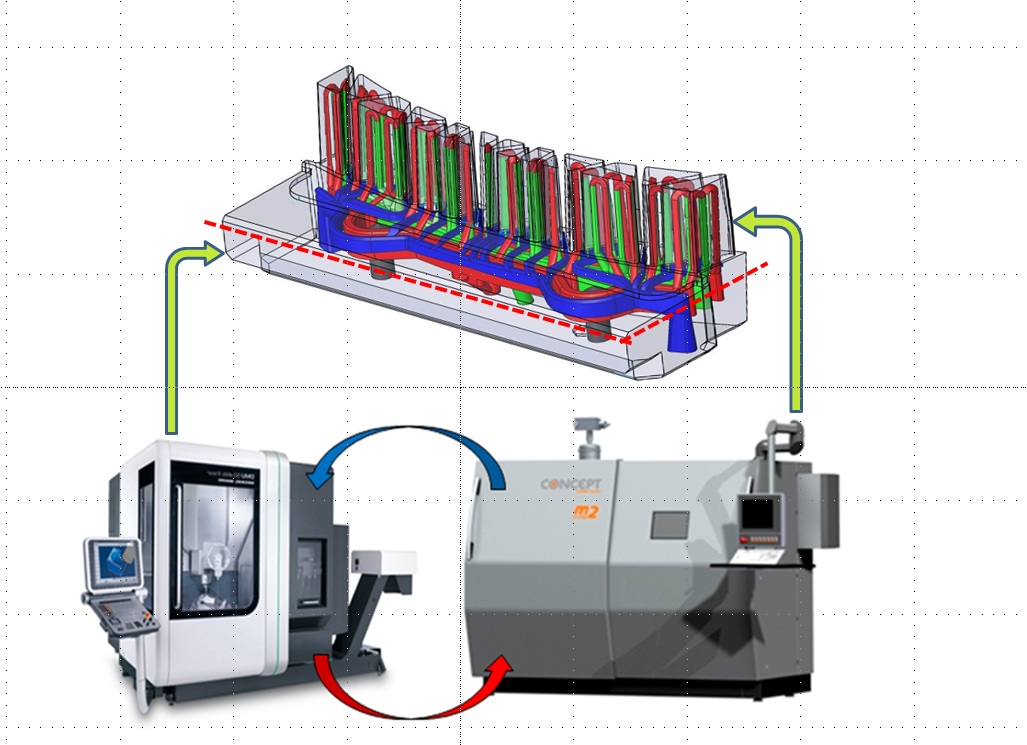
Related topics
ICT Research & Innovation Innovation Advanced manufacturing & processing Denmark Finland Germany Sweden Norwaydate: 10/06/2014
Project: Intelligent and Customized Tooling
acronym: IC2
See also: CORDIS
Contact: Contact
He reports that the EU-funded project has met its goals, improving tool performance and productivity and thereby reducing the need for additional tooling and equipment. While the tools are not necessarily cheaper, these advances can reduce the total cost of tooling by up to 30%.
More specifically, IC2 developed three new protective, wear-resistant coatings, designed innovative technology for the production of tooling. The project team also refined the use of embedded sensors for process optimisation. It also produced guidance on suitable business and organisational approaches for tooling manufacturers. According to Gellein, these recommendations, in combination with the new products and techniques developed by IC2, can significantly reduce the time needed to produce new tools for customers.
Leveraging knowledge
IC2’s technical advances improve the tools and the manufacturing process, and they also boost the quality of the products. The new coatings, for example, enhance the surface of the tool and notably its release properties.
“When you produce a plastic component,” Gellein explains, “the product has to be released from the tool once the process is finished. One common challenge is that the product can stick to the tool.”
But, he adds, IC2 had a second reason to work on new coatings. The partners also needed them to embed sensors on the surface of the tool. These sensors help to secure accurate information about the temperature in the tool cavity.
They enabled the team to design and validate one of its key achievements: a tool insert with a sophisticated in-built cooling and venting system. This innovative part was produced in a prototype of a hybrid manufacturing cell (HMC), a production unit combining two very different manufacturing approaches, which was also developed by the project.
Innovative long-life tools
“The use of sensors,” says Gellein, “made it possible to develop a design addressing some of the problems affecting current tools. Equipment based on this advanced and complex design could then be manufactured in the HMC prototype.”
IC2’s HMC is a combination of an additive manufacturing machine with a conventional milling machine. Additive manufacturing builds objects by successive addition of material, while milling is a subtractive process that removes material from a workpiece by means of rotary cutters.
The HMC is a way of bringing together the best of both techniques, says Gellein: “Conventional milling is an effective high-speed manufacturing technology, but it is limited in regards to producing complex geometries, such as internal cooling and venting channels. Additive manufacturing does not have the same limitations, but is more time-consuming and costly.”
Combining the two seamlessly and cost-effectively in a highly automated manufacturing cell means that milling techniques can be used to create the simpler parts of a tool, and additive manufacturing for its more complex features.
The HMC has permitted significant performance enhancements, says Gellein. In September 2013, when the project ended, a partner testing an insert made using the HMC reported that it had produced four times as many parts as its conventionally produced predecessor, without any signs of wear or damage. The insert was still in use seven months later.
Benefits beyond plastic
Gellein attributes the project’s success primarily to the enthusiasm and commitment of the team. “We managed to have a very strong group of people dedicated to the same goal,” he says.
IC2’s achievements are relevant to other manufacturing processes, he adds. The partners are planning to launch a new project to develop similar approaches for die casting aluminium and zinc.