Nature’s gift to automakers: self-cleaning plastics
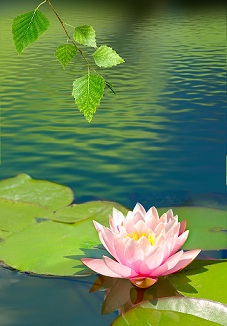
date: 14/01/2014
Project: Optimisation and upscaling of self-clean...
acronym: NANOCLEAN
See also: Info-centre
Contact: http://www.nanoclean-project.eu/
Technological innovation has often sought inspiration from nature. The hook-and-loop fasteners invented by Velcro, for example, use burrs and hooks similar to those found in certain plants to disperse seeds. Now an EU-funded project has successfully transferred the self-cleaning properties of the lotus plant to plastics.
The leaves surrounding the lotus flower are remarkable. Waxy water-resistant nanostructures on the surface – known as micropillars – ensure that rainwater washes off dirt without leaving any traces. Scientists behind the NANOCLEAN project wanted to see if these nanostructures could be synthetically engineered and applied to the surface of plastics used in cars.
“One of the main conclusions of our research is that micro- and nano-textures can be applied to three-dimensional (3D) curved surfaces, and that these textures are durable,” says project coordinator Dr Mónica Solay. NANOCLEAN’s prototypes, she reveals, demonstrated easy-to-clean properties, as well as optical effects that could be used for other applications.
NANOCLEAN’s technology results in an end-product that requires no further treatment, which could mean substantial savings in production. This is an important consideration, at a time when competition from countries outside the EU represents a significant threat.
“The technology also results in a lower cost to the environment,” adds Dr Solay. “The chemicals used as coatings for products that do not have this finish are often harmful to the environment.”
In this way, the project is meeting EU priorities of encouraging industrial innovation and using our resources more efficiently.
Scaling up self-cleaning surfaces
A curved plastic wing mirror mould was developed for trial. Pulsed lasers were used to develop the synthetic nano-structure, which was then directly reproduced on the plastic wing mirror casing using injection moulding.
The success of this procedure was highly significant, as it opens the door to wider production of ‘functional surfaces’ like this. Indeed, NANOCLEAN wanted to show that the mass-production of self-cleaning, 3D complex plastic components was possible.
The project, which was completed in September 2012, brought together a pan-European team that included some of the most respected specialists in their field. This proved to be central to the success of NANOCLEAN, since it involved European companies with international profiles, such as FIAT Research Centre in Italy and BASF SE in Germany, and effectively created a potential international sales network for the technology.
The success of the project enabled the setting up of several small companies, which are taking the results of the research to the market.
“Several target sectors of NANOCLEAN have already expressed interest in the technology, which gives us hope for its successful commercialisation,” concludes Dr Solay.