Modular, flexible, sustainable: the future of chemical manufacturing
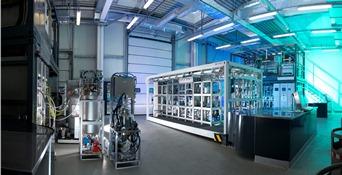
CoPIRIDE and F³ Factory are two of the projects that have developed innovative technologies to support the shift towards greater versatility and smaller environmental footprints. They have produced new technologies, processes and manufacturing concepts that will feed into the design and operation of innovative chemical plants. The results of their work have the potential to provide the chemical industry with a much-needed competitive boost.
Small plants, huge potential
The achievements of CoPIRIDE include patents on gasification, catalyst system and reactor fabrication technology.
“CoPIRIDE has contributed to improving the competitiveness of the European chemical industry and will help to secure jobs by providing smart, moveable and flexible chemical plant concepts,” says project coordinator Dr Patrick Löb, head of the Mixing and Fine Chemistry Department at the Institut für Mikrotechnik Mainz.
“For example,” he adds, “a chemical plant embedded in a 3-by-12-metre container is more capable of adapting to market trends and bringing process and product innovations faster to market.”
The team developed novel miniaturised reactors (micro-reactors) — designed to fit inside these garage-sized plants — that give operators far better control over chemical reactions. This advance will lead to more sustainable processing, with fewer inputs of energy and raw materials.
Tried and tested
To ensure that CoPIRIDE’s findings were relevant across the industry, the project’s research teams were grouped around specific chemical processes.
“Piloting activities were carried out to demonstrate results and show improvements in the chemical process itself,” explains Dr Löb.
One demonstration involved a chemical factory embedded in a special flexible and moveable container. The move from drawing board to bricks and mortar required two different facilities, each equipped for a different process step. Once up and running at an industrial site in Germany, the plants were able to produce a large batch of a particular chemical.
Another demonstration addressed the need for lower production ranges. This required a modular multi-purpose ‘mini-plant’, the construction of which was led by a consortium partner from the small and medium-sized enterprise (SME) sector.
A separate demonstration plant was set up to allow researchers to explore the feasibility of producing biodiesel from waste oils in supercritical conditions. The demonstration targeted cost efficiency, greater competitiveness and improved sustainability compared to other starting materials and processing conditions.
The gasification of biomass to produce chemicals and ammonia (which can then be processed into fertiliser) was also trialled.
In addition, the project team sought to improve processing approaches. They looked into a concept known as ‘Novel Process Windows’, which aims at reducing reaction time through a highly intensified approach that better exploits chemical reactivity.
“Quite unique to the CoPIRIDE project has been that, from the beginning, simplified cost analysis and lifecycle assessments have been performed to judge the different processing or production options,” says Dr Löb.
A wide variety of partners were involved in the project, establishing a pan-European cooperation that should help ensure widespread dissemination of the outcomes throughout Europe’s chemical industry.
Cleaner, leaner, faster processes
The F³ Factory project’s vision for the chemicals plant of the future focused on reconciling the seemingly conflicting requirements of flexibility and resource efficiency.
It translated into the development of a standardised, modular type of plant designed for easy deployment throughout the industry – a ‘plug-and-play’, container-based production facility. In addition to their work on the equipment, the partners designed software to facilitate and streamline the design of new processes.
The outcomes offer intriguing possibilities. The partners estimate that their technology can, for example, reduce time-to-market by up to 50%, cut operating expenses and capital expenses by as much as 20% and 40% respectively, and potentially halve the environmental footprint of individual processes.
The team’s work aimed at a modular and container-based platform providing the prerequisites for a variety of chemical process types (e.g. polymers, health care and agrochemicals), in contrast to conventional bulk processing technology that is tailored to just one type of feedstock or process, but cannot readily be used for another.
To optimise their innovative plant, the participating chemical companies, academic organisations and equipment manufacturers also seized opportunities for process intensification. “We were able to boost the efficiency of various process steps by orders of magnitude,” says project coordinator Dr Sigurd Buchholz of Bayer Technology Services.
Consensus for change
In addition, they harmonised production practices among the participating industrial partners sufficiently to ensure that the resulting technology would work for them all. This open and enthusiastic cooperation among major chemical companies, says Dr Buchholz, was one of the project’s main assets. The project, he adds, was a strategic endeavour for all participants.
“The fascinating thing,” he notes, “was that people left the competitive environment and got together on a joint environment, to develop technology that they could all enjoy.” He is convinced that this collaborative approach could hold the key to similar advances in other industries.
To demonstrate that its production technology could place the EU’s chemical industry ahead of the curve, F³ Factory moved from theory to practice by building a model factory – the INVITE Research Center.
Located in Leverkusen, Germany, this standardised platform was trialled successfully by the industrial partners involved in the project.
“We had seven different major chemical companies preparing their processes and operating these in the respective process containers on one single site,” Dr Buchholz reports.
What does the future hold for the F³ Factory technology? Further work is being carried out to prepare it for widespread deployment, and a number of partners are planning to adopt it alongside existing facilities. The model factory INVITE is now being operated by a separate legal entity –and remains available for open innovation and any company to use.
Like CoPIRIDE, F³ Factory ended in August 2013, leaving a legacy of innovation that will help to take the EU’s chemical industry another step ahead.
Video in German below